What Is SFM? A Complete Guide To Surface Feet Per Minute In Machining
SFM, meaning Surface Feet per Minute in CNC machining, measures how fast a cutting tool moves across a workpiece. It is expressed in feet per minute. SFM combines the tool or workpiece diameter with the spindle speed (RPM). A larger diameter or higher RPM results in a higher SFM.
Machinists use surface feet per minute to determine the best cutting speed for a material. Different materials have recommended SFM values for optimal performance. For example, 303 annealed stainless steel has an SFM of 120 when using high-speed steel tools.
Why SFM Matters In CNC Machining?
SFM in machining is a very important factor. It tells us how fast the cutting tool moves across the surface of the material. Getting this speed right helps ensure quality, tool life, and efficiency. Below are the main reasons why SFM matters:
1. Tool Life
If the SFM is too high, the tool can overheat quickly, leading to rapid dulling or even cracking and breakage. On the other hand, if the SFM is too low, the tool may rub against the material instead of cutting it effectively, causing excessive wear.
Choosing the right surface feet per minute means the cutting tool lasts longer. This saves you money on new tools and time to change them. So, good SFM means better tool health and lower cost.
2. Surface Finish
SFM controls how smooth the final surface of the material will be. A correct cutting speed makes cleaner cuts. But if it’s too fast or too slow, the surface will be rough, burnt, or wavy.
In industries like aerospace or medical parts, a fine surface is very important. If the surface finish is poor, the part won’t meet quality standards. Getting SFM right avoids rework and waste.
3. Cutting Efficiency
With the right SFM in machining, materials can be removed in less time. This means the process is faster without harming the tool or material.
This is especially helpful in production projects. If SFM is optimized, more parts can be made in less time, which means more productivity and lower cost per part.
4. Changes Based on Material
Different materials need different cutting speeds. For example, aluminum can be cut at high SFM because it’s soft, while steel needs slower SFM because it’s hard. If you use the wrong SFM for the material, you’ll damage both the tool and the workpiece.
5. Works with Other Settings
SFM is tied to RPM (revolutions per minute) and the size of the tool or workpiece. You can’t just set one without thinking about the others.
If the diameter of the cutting tool increases, the RPM must be reduced accordingly to maintain a consistent SFM. If you don’t, the tool will spin too fast and overheat. Understanding how SFM fits into the whole setup helps avoid mistakes and keeps the machine running smoothly.
Differences Between SFM And RPM
Understanding the difference in SFM meaning and features between RPM (Revolutions per Minute) is key, as they serve different purposes. Here are the differences:
Units of Measurement
SFM (Surface Feet per Minute) is measured in feet per minute. It’s how fast the edge of the tool moves across the material’s surface. RPM (Revolutions Per Minute) is measured in rotations per minute. It’s how many times the tool spins in one minute.
These are different kinds of speed. SFM is the actual cutting speed at the edge of the tool, while RPM is just the spinning speed.
Relation to Tool Diameter
Tool size matters when it comes to SFM and RPM. If the tool is bigger, the edge travels further each time it spins. So, SFM is higher at the same RPM.
If the tool is smaller, the edge moves less, so SFM is lower at the same RPM. So when the tool diameter changes, the RPM must be adjusted to get the right SFM.
Machine Settings
RPM is what the machine uses. You enter this value in the control system.
SFM is not a machine setting. It’s used to calculate the right RPM based on the tool size and material. The machinist or CAM software figures out the right SFM for the job, then converts it into an RPM value for the machine.
Effect on Machining Quality
Using the right SFM is important for good cutting. It helps avoid overheating, tool wear, or poor surface finish. If SFM is too high or too low for the material, you’ll get damaged parts or broken tools.
RPM alone doesn’t guarantee good results. The right RPM must be chosen based on the right SFM. If RPM doesn’t match the tool size and material, you’ll get bad cuts or reduced tool life.
How to Convert SFM to RPM?
When you’re working with CNC machines, you often get the cutting speed in SFM (Surface Feet per Minute). But the machine needs you to enter RPM (Revolutions per Minute). So, you have to convert SFM to RPM, and it’s not hard if you follow a simple formula.
The Basic Formula: To change SFM to RPM, you can use this formula:
RPM = (SFM × 3.82) ÷ Tool Diameter (in inches)
What the Numbers Mean:
3.82 is a constant that helps convert feet per minute into revolutions per minute.
SFM Formula And Calculation
SFM is an essential factor in setting the right cutting conditions for your material and tool. Aside from using SFM compiler, you can calculate it precisely using the formula below:
Calculating SFM
Calculating SFM would require two things:
- RPM (Revolutions per Minute) of the tool or part
- Diameter of the tool or part in inches
Here’s the formula: SFM = (RPM × Tool Diameter) ÷ 3.82
Here’s a breakdown:
- Multiply the RPM by the tool’s diameter (in inches)
- Then divide the result by 3.82 (a constant used to convert inches and minutes into surface feet per minute)
Example SFM Calculations for Milling and Turning
Here are the two main examples—one for milling and one for turning.
Example 1: Milling
Tool diameter: 1 inch
Spindle speed: 1000 RPM
Using the formula: SFM = (1000 × 1) ÷ 3.82 = 261.78 SFM
So your cutting speed is about 262 surface feet per minute.
Example 2: Turning
Part diameter: 2 inches
Spindle speed: 800 RPM
Using the same formula: SFM = (800 × 2) ÷ 3.82 = 418.32 SFM
So in this case, the SFM is about 418.
These examples show how SFM changes with the size of the tool or part and the RPM. Even a small change in diameter can make a big difference.
Using SFM Calculators and Charts
If you don’t want to do the math every time, you can use SFM calculators or charts. These are available online, in machining apps, or even in tool catalogs. You just enter the tool size, and it helps convert the SFM to RPM, giving you the answer right away. The charts are also great, and they have recommended SFM values for different materials (aluminum, steel, titanium, etc.). You find your material on the chart, see the SFM, and then calculate the RPM for your tool.
Using calculators and charts saves time, reduces errors, and helps you work more safely and efficiently. Here are some examples of SFM calculators you can use for assistance:
- Machinist’s Calculator
- Online SFM Calculators
- CNC Machine Software
Units And Standards For SFM
When working with different machines or metal cutting, SFM (Surface Feet per Minute) is the way to measure cutting speed. Using tools like the SFM compiler tells you how fast the cutting edge of your machine moves over the material. But you’ll find SFM measured in different units, depending on what system you’re using. Knowing those units helps you read charts, use calculators, and follow guidelines to correctly know the depth of cutting in machining.
Imperial (FPM) vs Metric (M/Min) in SFM
In machining, you’ll come across two main unit systems. There’s the Imperial System (mostly used in the U.S.), where SFM is measured in feet per minute (FPM). That means how many feet of material your CNC cutting tool touches each minute.
The Metric System (used in Europe, Asia, and many other places) measures the same concept in meters per minute (m/min). It’s the same idea, just with different units.
So, if you know SFM in feet per minute, you can multiply by 0.3048 to get meters per minute. Or if you have m/min and want to convert to feet per minute, you multiply by 3.281. Both units measure surface cutting speed. Knowing which one you’re using is key to avoiding the wrong settings.
That conversion factor—0.3048 meters per foot—is one you’ll need to keep. Knowing both units will make you a more versatile machinist.
Industry Standard SFM Ranges by Material
Different materials need different cutting speeds. Some are soft and can be cut fast, others are hard and need to be cut slowly to avoid damaging the tool. Industry charts will often show recommended SFM ranges for each material. Here are some general examples in Imperial:
- Aluminum: 300 – 1000 SFM (It’s soft, so it can be cut fast.)
- Mild Steel: 100 – 300 SFM (Stronger than aluminum, it needs to be cut slower.)
- Stainless Steel: 50 – 200 SFM (Harder and tougher, it needs to be cut even slower to protect the tool.)
- Titanium: 30 – 70 SFM (Very hard to cut; slow speeds help reduce heat and wear.)
- Plastics: 500 – 1500 SFM (These cut easily, but too much heat can melt them, so speed must be managed.)
These numbers aren’t exact for every situation. They depend on other things like tool type, coating, coolant, and machine strength. But they’re a good starting point.
Factors That Affect SFM Settings
Choosing the right SFM is important because it affects the finish, tool life, and how fast the job gets done. Here are the main things that affect the SFM setting:
1. Material
Different materials need different speeds. Softer materials like aluminum can be cut at higher SFM because they are easier to machine. Harder materials like stainless steel or titanium need slower speeds to avoid burning the tool or overheating the workpiece.
2. Tool
The tool itself matters. Tools made from carbide can handle higher speeds than tools made from high-speed steel (HSS). Carbide tools are harder and stay sharper longer so they can cut faster without wearing out too quickly.
3. Tool Diameter
The tool diameter changes how fast it can spin. A larger tool spins faster at the outside edge even if the spindle speed (RPM) stays the same. That’s why the tool diameter must be considered when setting the SFM. Larger tools need lower RPMs to stay within the right SFM range.
4. Coolant and Lubrication
Using coolant or cutting fluid reduces heat and friction. With coolant, the machine can run at higher SFM without burning the tool or the material. Without it, the cutting speed may need to be reduced to keep temperatures safe.
5. Machine
Different types of CNC machines have their own limits. Some machines can’t reach high spindle speeds, others may not be rigid enough for high-speed cutting in hard materials. The machine’s power and stability will affect how high you can safely set the SFM.
SFM In CNC Programming
In CNC programming, SFM values are essential for defining spindle speed settings in G-code. Programmers must choose an SFM appropriate for the material and tool type, then convert it into RPM using the tool diameter. Once the correct RPM is calculated, it’s programmed into the toolpath to ensure the machine runs at the optimal speed.
How CAM Software Handles SFM?
CAM software not only creates toolpaths for CNC machines but also plays a critical role in optimizing cutting parameters like Surface Feet per Minute (SFM). Most CAM systems allow users to input the workpiece material and cutting tool type. Based on this input, the software draws from material-specific databases to recommend an ideal cutting speed.
By accurately calculating SFM and converting it into the appropriate RPM based on tool diameter, CAM software helps ensure that the spindle speed is neither too slow (leading to inefficient cutting and poor surface quality) nor too fast (causing premature tool failure or thermal damage to the part).
In addition, manual SFM calculations often vary between operators and can introduce errors, especially in complex geometries or high-tolerance parts. Using CAM for machining removes this variability, improving cycle times, tool life, and product quality.
SFM in G-code
G-code is the language the CNC machine understands. It tells the machine what to do, like how fast to spin, where to move, and how deep to cut.
Even though SFM itself doesn’t show up in the G-code, it’s used to calculate the correct spindle speed (RPM), which does show up in the code (usually with an “S” followed by a number, like S1500). So when you see a spindle speed in G-code, that value comes from converting the SFM to RPM based on the tool’s size.
Precision Machining With Optimized SFM At Wshxing
At Wshxing, with expert knowledge of CNC machines and SFM to deliver high-quality CNC machining services. By selecting the suitable cutting speed for each material and tool, we ensure fine surface finishes, high precision, and maximum efficiency. Whether you’re working with aluminum, steel, or complex plastics, our precision CNC machining capabilities guarantee consistent, cost-effective results to meet your project needs.
Conclusion
So, what is SFM? It’s more than just a number, it’s how well you know the material, the tool, and the machine. By paying attention to it, you’re not only improving the quality of your work but also the whole process. Whether you’re new to machining or already hands-on, treating SFM as a design choice, not just a setting, will help you get better results.
FAQs
Is SFM the same as cutting speed?
Yes, SFM (Surface Feet per Minute) is just another way to say cutting speed. It tells you how fast the edge of the tool moves across the surface of the material while cutting. The faster the edge moves, the higher the cutting speed.
Can I use one SFM setting for all materials?
No, you can’t. Different materials need different cutting speeds. Softer materials like aluminum can handle higher SFM. Harder materials like stainless steel or titanium need lower SFM to avoid overheating and tool damage.
What’s the fastest way to calculate SFM?
The quickest way to calculate SFM is to use a simple formula:
SFM = (Tool Diameter × RPM × 0.262)
This works if your tool size is in inches. If you know the tool diameter and the spindle speed (RPM), you can plug them into the formula and get the SFM. You can also use a calculator or software that does it for you.
Recommendations
How To Create A Prototype With Steps: An Expert Guide
A prototype is an early version or physical model of a product idea that manufacturers can test and refine before investing in mass production. It acts as a product template and provides a practical approach to understanding a product’s appearance and function before production. When developing a product, product teams create a product prototype to test the product’s usability, design, and performance, gather user feedback, identify potential issues in the early stages, and identify possib...
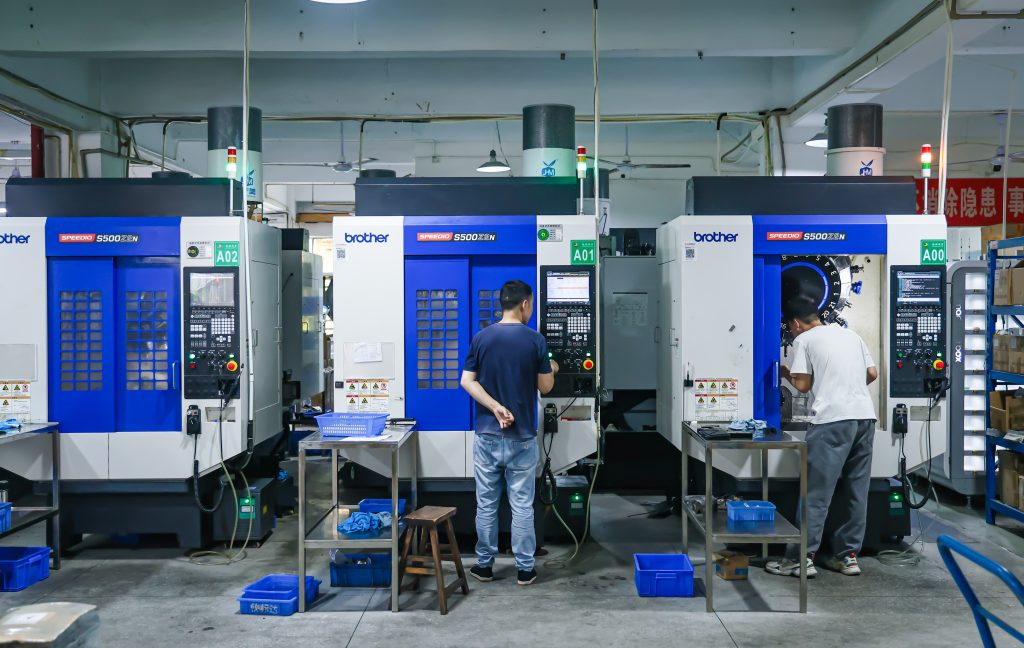
Press Fit Tolerance: Defination, Practices, And Calculation
The manufacturing industry is highly precision-centric, where even the slightest of margins can create huge differences in product quality, cost, and utility. This article discusses the topic of press fitting, where a few micrometers of deviation dictates the criterion for part failure. So, what is press fit and, the factors influencing press fit tolerancing, and present an example of a press fit calculator. We will also share some key tips to keep in mind while designing components for p...
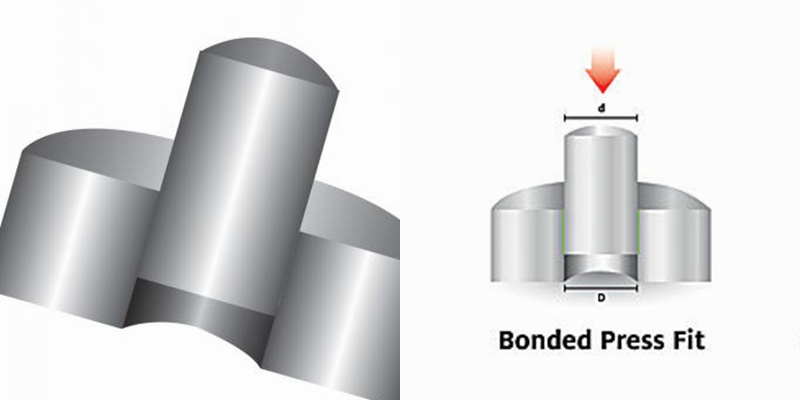
Cost Of CNC Machining: What Affects & How to Save It?
CNC machining is a technique used to make precision parts and replicate amazing designs. There are a lot of advantages of CNC machining, such as increasing the speed of parts production. It also reduces human errors during manufacturing as it is being controlled by the computer. However, many people do not seem to understand the rationale behind its cost. The machine and material you use can affect the price. Today, many customers still struggle with CNC machining cost calculation. With t...
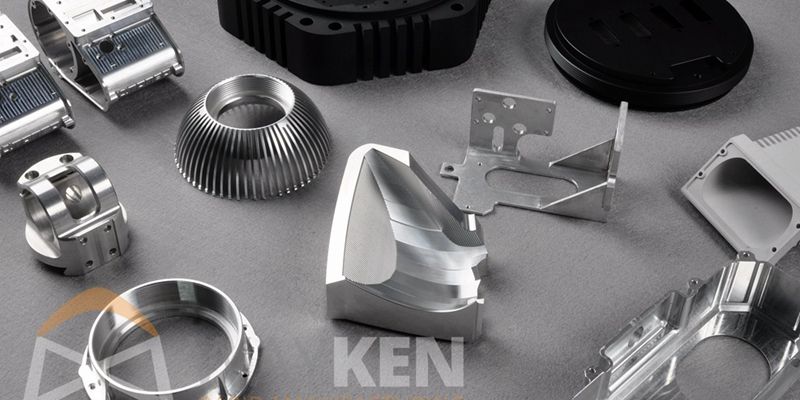